BIS ZUM MARS
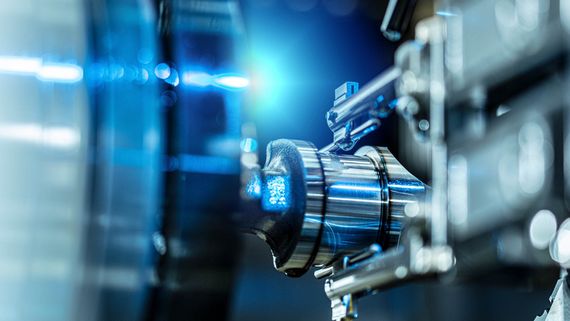
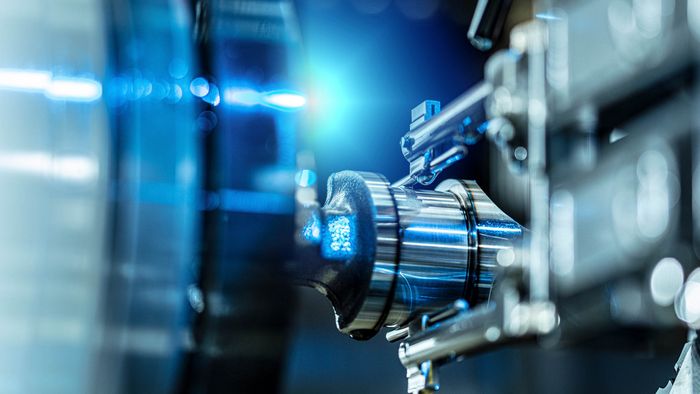
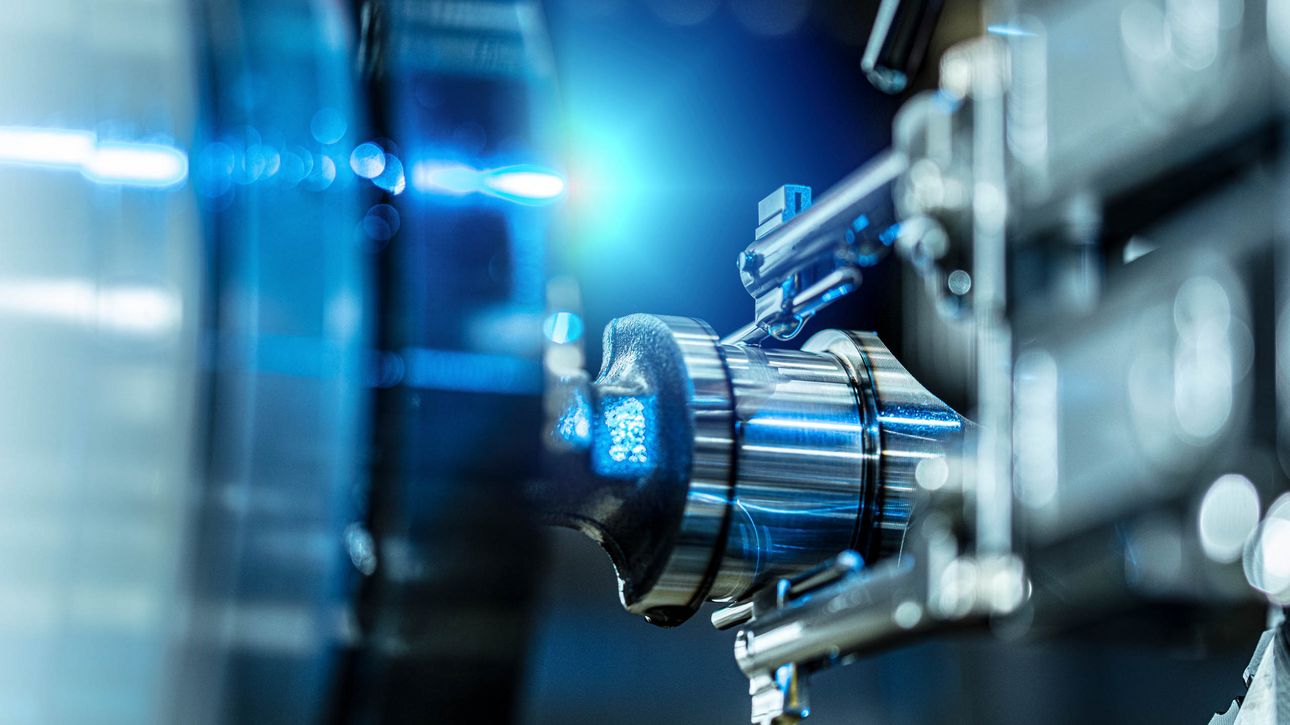
EIN UNSCHEINBARER GRAUER KASTEN steht auf dem roten Mars-Sand. Rauch steigt aus der Satellitenanlage auf. Von einem Raumschiff aus steuert Alexander Gerst den Roboter Rollin’ Justin. Der öffnet die Anlage auf der Oberfläche des Mars. Er identifiziert das qualmende Modul und ersetzt es durch ein neues. Über ein Tablet bestimmt der Astronaut, welche Arbeitsschritte der Roboter dabei auszuführen hat. Fertig! Die Kommunikation mit dem roten Planten ist gesichert. Zugegeben, das war nur eine Simulation. Der Roboter war im Raumzentrum im deutschen Oberpfaffenhofen im Einsatz, Alexander Gerst immerhin hat ihn von der Internationalen Raumstation ISS aus gesteuert. Tatsächlich gelten intelligente Roboter als entscheidender Faktor bei der Entdeckung und Erschließung ferner Planeten. Und möglicherweise käme mit Rollin’ Justin oder einem seiner Kollegen ein Stück Schleiftechnik der UNITED GRINDING Group auch auf dem Mars zum Einsatz. Sogenannte Robot Speed Reducer Gears werden in den Gelenken von Robotern eingesetzt. Diese Reduktionsgetriebe verringern die Drehzahl des Motors, der die Gelenke antreibt. Ohne sie wäre der Roboter nicht in der Lage, dosierte Bewegungen auszuführen. „In der Kombination aus Wirtschaftlichkeit, Leistungsfähigkeit und Bearbeitungsqualität kann kein anderes Fertigungsfahren dem Schleifen das Wasser reichen“, erklärt Prof. Dr. Konrad Wegener vom Institut für Werkzeugmaschinen und Fertigung der ETH Zürich. Die Robot Speed Reducer Gears illustrieren das eindrucksvoll: Halbkreisförmige Nuten mit einer Durchmessertoleranz von +/- 3 μm werden in die Gelenke geschliffen. Gefertigt wird 24/7 und mannlos. „Etwa 2,5 Millionen solcher Getriebe werden jährlich mit Maschinen von MÄGERLE geschliffen“, schätzt Produktmanager Viktor Ruh.
DREI KRITERIEN
Schleifen als spanendes Fertigungsverfahren ist eine uralte Technik. Schon in der griechischen Antike wurden Schleifsteine mit Wasser oder Öl gekühlt. 1845 kam die erste Rundschleifmaschine auf den Markt. Und in den 174 Jahren seither hat das Fertigungsverfahren nichts an Relevanz eingebüßt. „Der Prozess glänzt heute durch höchste Abtragsraten, kurze Zykluszeiten und minimalen Verschleiß des Werkzeugs. Dies bietet keine andere Technologie“, fasst Harri Rein zusammen. Rein ist CTO der Technologiegruppe Tool. Daniel Huber erfüllt diese Funktion für Cylindrical, Daniel Mavro für Surface & Profile. Zusammen mit Christoph Plüss, Chief Technology Officer der Unternehmensgruppe, bilden sie das CTO-Board, das die Leitplanken für die technologische Entwicklung der acht Unternehmensmarken festlegt.
Nicht nur in der Robotik, auch in der Mikroelektronik kommt Schleifen zum Einsatz. Die sogenannten Wafer, Halbleiter, die als Grundplatte für elektronische Bauelemente dienen, werden geschliffen. In innovativen Technologien wird der Einsatz neuartiger Materialien oft erst durch die entsprechenden Bearbeitungsverfahren möglich. Keramische Verbundstoffe etwa in Triebwerken der Aerospace-Industrie können am besten durch Schleifen bearbeitet werden. „Leichtbauteile für den Automobil- oder Flugzeugbau aus kohlenstofffaserverstärktem Kunststoff werden mit PKD-Werkzeugen bearbeitet, die vorher einen Schleifprozess durchlaufen haben“, erklärt Huber.
VORTEILE IN DER ANWENDUNG
Die hohe Bearbeitungsqualität des Schleifens realisiert zahlreiche Vorteile in den industriellen Anwendungen „Feinere Oberflächengüten im Automobilsektor führen zu weniger Reibung und dadurch einen höheren Motorwirkungsgrad“, so Mavro. „Engere Toleranzen in der Luft- und Raumfahrtindustrie steigern den Wirkungsgrad von Triebwerken, zum Beispiel durch Reduzierung der Kühlluftstromverluste.“ Im Automobilbereich etwa bieten die Marken der Unternehmensgruppe zahlreiche innovative Anwendungen. Etwa das Schleifen von Ausgleichswellen auf einer SCHAUDT ShaftGrind S. Diese sorgen für Laufruhe in einem Verbrennungsmotor, indem sie Gegenfrequenzen erzeugen. Sie sind weder gerade noch zylindrisch – und stellen damit für die Bearbeitung eine große Herausforderung dar. Oder die Bearbeitung von Lenkzahnstangen auf einer MÄGERLE MFP, bei der bis zu acht Werkstücke in einer Aufspannung mit Profiltiefen bis zu elf Millimetern und Breiten bis zu 300 Millimetern geschliffen werden – was eine extreme Herausforderung an die Spindelleistung und die Stabilität der gesamten Maschine darstellt.
MESSEN UND SCHLEIFEN
Der eigentliche Schleifvorgang lässt sich mit angrenzenden Prozessen wie dem Messen oder Abrichten verknüpfen. „Hier kann eine Schleifmaschine mit einer Messmaschine als Zelle aufgebaut werden, die mittels eines Roboters als Schnittstelle beschickt wird“, so CTO Rein. Das Ergebnis ist eine mannlose oder auch „Lights out“-Produktion, mit der massenhafte Stückzahlen zu realisieren sind. Im Internal Measuring System IMS von WALTER etwa lassen sich die Parameter der zu produzierenden Werkzeuge hinterlegen. Bei Abweichungen reguliert das System den Bearbeitungsprozess nach oder stoppt die Produktion, wenn der Toleranzbereich verlassen wird. „Auch bei kleinen Losgrößen oder Einzelwerkstücken ist das In-Prozess-Messen wichtig, um sofort die geforderte Genauigkeit zu erreichen“, erklärt Huber. Das Abrichten sorgt dafür, dass der Verschleiß der Schleifscheibe kompensiert wird. Damit werden über den gesamten Produktionszyklus die exakt gleichen Werkstücktoleranzen und die gleiche Qualität garantiert. „In bestimmten Anwendungsbereichen werden zunehmend härtere Werkstoffe wie Keramik eingesetzt, die nach Superabrasives verlangen und diese wiederum brauchen eine hochfeste, also metallische Bindung der Schleifscheibe“, erklärt Wegener. Und für eine metallisch gebundene Schleifscheibe ist die WireDress®-Technologie das Mittel der Wahl zum Abrichten. Nach dem Prinzip der Drahtelektroerosion wird damit die Schleifscheibe berührungslos abgerichtet. Das Ergebnis ist maximaler Kornfreistand und optimale Schnittigkeit. „Ich glaube, dass WireDress® metallisch gebundenen Schleifscheiben zum Durchbruch verhelfen wird“, so Wegener, dessen Institut die Technologie gemeinsam mit STUDER entwickelt hat.
DER MENSCHLICHE FAKTOR
Ein weiterer wichtiger Faktor, der das Ergebnis des Schleifprozesses bestimmt, ist der Mitarbeiter. „Sein Erfahrungsschatz ist von großer Bedeutung“, betont CTO Rein. Deshalb investieren alle Unternehmen der UNITED GRINDING Group stark in die Aus- und Weiterbildung ihrer Mitarbeiter (siehe dazu auch Seite 36 ff.). Das menschliche Know-how wird auch im Zuge der weiteren Digitalisierung seine Bedeutung behalten. „Einerseits muss das Erfahrungswissen der heutigen Schleifer in Assistenzsysteme und Datenbanken einfließen, andererseits werden zukünftig anspruchsvollere Aufgaben auf den Operator zukommen“, so Huber. Denn: „Bei einer komplexen Fertigungszelle braucht der Bediener Fähigkeiten eines ganz anderen Niveaus“, ergänzt Mavro. Und so hat sich die UNITED GRINDING Group Zweierlei vorgenommen: immer bessere Technologien und immer bessere Mitarbeiter. Beides führt schließlich zu immer besseren Schleifergebnissen.