PROFILE IN GLAS
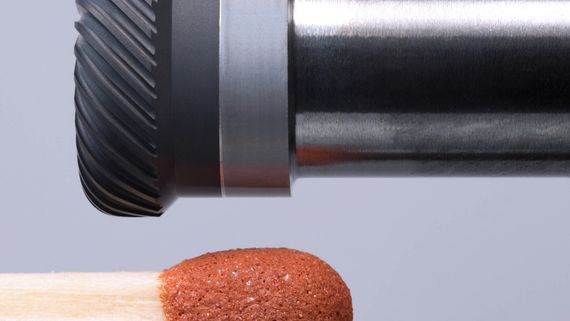
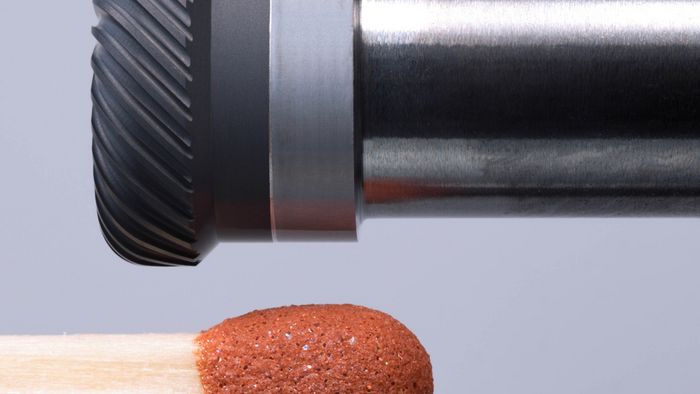
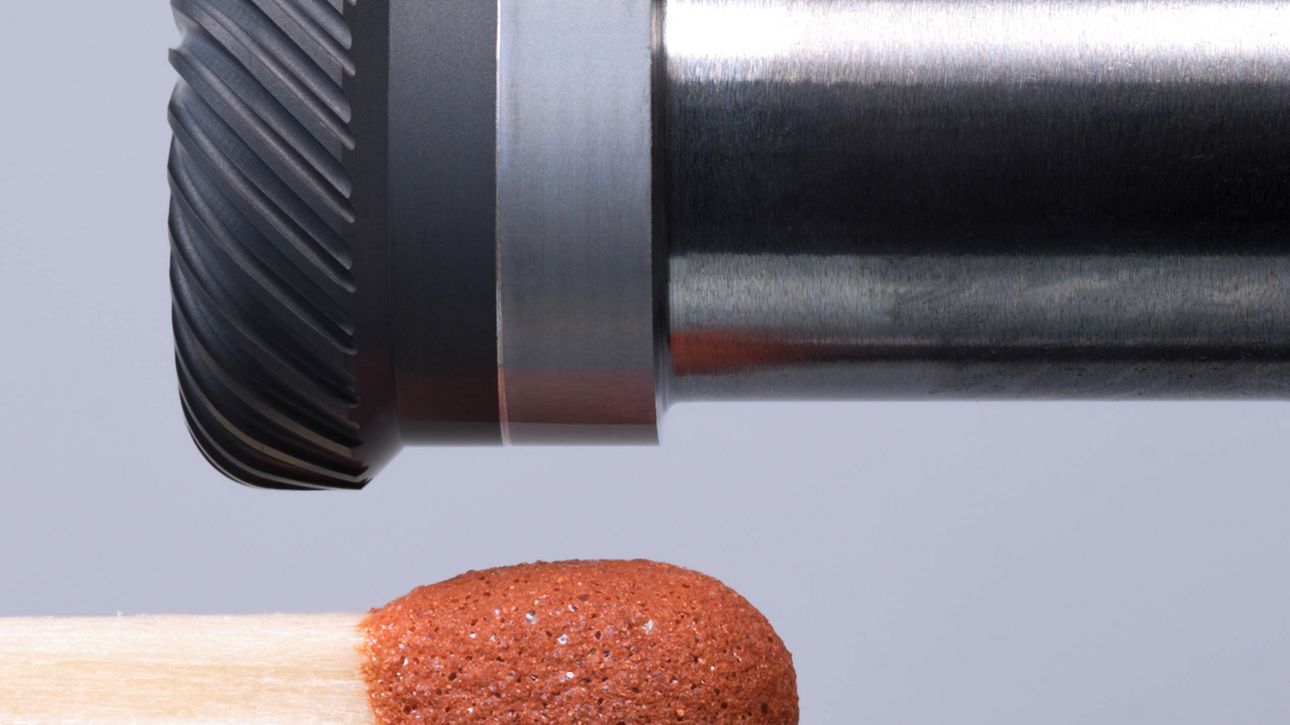
ES IST EIN REGELRECHTES WETTRENNEN: Welcher Hersteller bringt seine neue Smartphone-Generation mit welchen Features auf den Markt? Schnellere Prozessoren, bessere oder mehr Kameras, ein größerer Bildschirm, Fingerabdrucksensor, Gesichtserkennung, abgerundete Metallgehäuse, ein Screen mit abgerundeter Kante. Die Hersteller Samsung, Huawei und Apple, die zusammen fast die Hälfte des Weltmarktes beherrschen, versuchen regelmäßig, die jeweiligen Wettbewerber zu übertrumpfen. Einen Coup in diesem Wettrennen landete der südkoreanische Hersteller Samsung im Frühjahr 2019, als er das weltweit erste Smartphone mit einem 5G-Mobilfunkchip auf den Markt brachte.
In den verschiedenen Geräte-Generationen steckt auf unterschiedliche Weise Know-how und Bearbeitungsleistung von WALTER und EWAG, den Werkzeugbearbeitern der UNITED GRINDING Group. Bei klassischen Handys wurde die Schale im Kunststoff- oder Metalldruckgussverfahren gefertigt. Die Druckgussformen dafür wurden in der Regel mit Werkzeugen gefertigt, die wiederum mit WALTER Maschinen hergestellt wurden. Nach der internationalen Abkürzung für Computer, Communication und Consumer Electronics werden diese 3C-Werkzeuge genannt.
PKD-PROFILFRÄSER
Seit den Smartphone-Generationen von iPhone 6 und Samsung Galaxy S5 kommt mehr und mehr die Bearbeitung durch per Laserverfahren hergestellte Werkzeuge zum Zug. Beim Apple iPhone 6 etwa wird die Verrundung am Aluminiumgehäuse mit PKD-Profilfräsern bearbeitet. Beim iPhone X dagegen ist Edelstahl im Gehäuserahmen verbaut. Mit diamantbelegten Werkzeugen wie PKD sind diese aufgrund der chemischen Affinität mit eisenhaltigen Werkstoffen nicht mehr zu bearbeiten, stattdessen kommen CBN-Fräser zum Einsatz. Auch diese Werkzeuge lassen sich mit Maschinen wie der EWAG LASER LINE ULTRA oder der LASER LINE PRECISION herstellen.
Mit neuen Anforderungen an Technik und Design wird nicht zuletzt auch mit dem Aufkommen von 5G-Smartphones immer mehr auf Materialien wie Glas und Keramik zurückgegriffen. Diese bieten eine Reihe von Vorteilen. Einer betrifft die Empfangsleistung der Smartphones: „Metallgehäuse schirmen grundsätzlich die Wellenausbreitung des Mobilfunks ab“, erklärt Andreas Bußmann, Experte für Endgeräte bei der Deutschen Telekom. Deshalb wird bei Geräten mit einem Metallgehäuse dieses als Antenne genutzt. „Dazu muss es aber von den anderen verbauten Metallteilen abgeschirmt werden. Das geschieht durch Plastikstege.“
DIREKT AUF DIE PLATINE
Diese Abschirmung entfällt bei Mobilgeräten mit einem Glas- oder Keramikgehäuse. „Ich kann die Antennen direkt auf die Platine aufsetzen. Das ermöglicht mehr bauliche Freiheiten“, so Bußmann. Und diese baulichen Freiheiten sind im Bereich von 5G sehr willkommen, weil hier in der Regel mehr interne Antennen ins Smartphone integriert werden. Die in Europa für 5G verwendete Frequenz liegt bei 3,5 Ghz (4G: 2,6 Ghz), in den USA und in Japan wird im Millimeter-Wave-Spektrum von 28 Ghz gefunkt.
Um diese Frequenzen zu empfangen, werden bis zu drei Antennen in die Smartphones integriert, im Bereich des Millimeter- Wave-Spektrums, das besonders sensibel ist und praktisch eine direkte „Sichtverbindung“ mit der Antenne braucht, sogar bis zu vier. Die Herausforderung liegt dabei nicht in erster Linie darin, die Antennen vom Bauraum her überhaupt in das Gerät zu integrieren, sondern darin, die Antennen so einzubauen, dass sie nicht durch den Körper des Users abgedeckt werden.
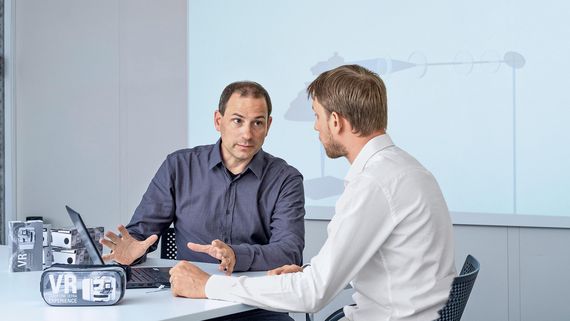
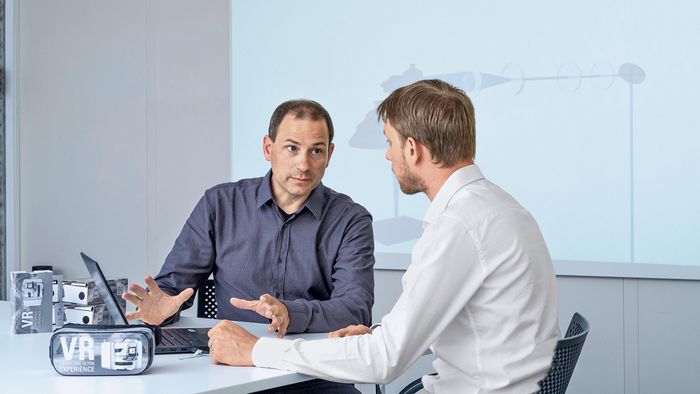
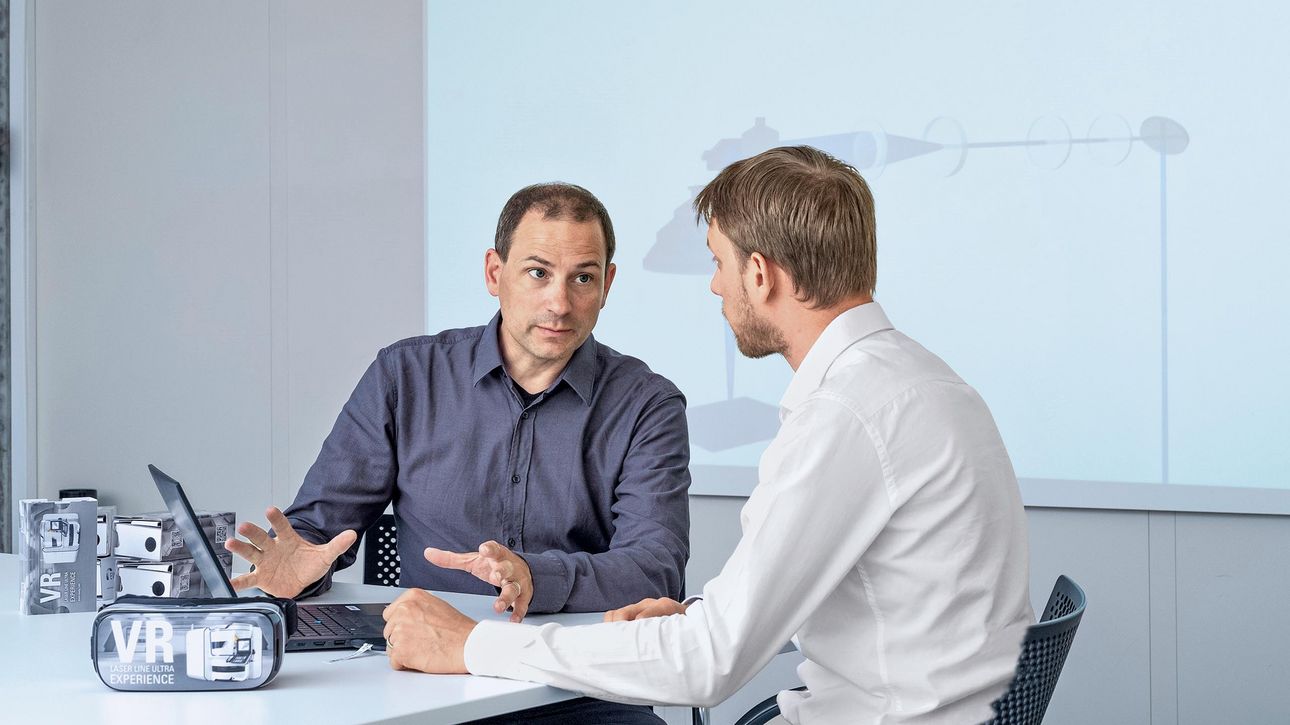
Darüber hinaus wirken Glas oder Keramik als Material für die Handyschale hochwertiger und nachhaltiger als etwa Kunststoff und erlauben im Design mehr Möglichkeiten. Ein Gerät wie das Samsung Galaxy S10 verzichtet außerdem deshalb auf einen Metallrücken, um ein kabelloses Laden des Gerätes per Induktion möglich zu machen. „Durch ihre Sprödheit, Härte und geringe Wärmeleitfähigkeit stellen Materialien wie Glas oder Keramik ganz besondere Anforderungen an die Qualität der Werkzeuge, mit denen sie bearbeitet werden“, erklärt Dr. Claus Dold, Leiter der Prozessinnovation bei EWAG.
HOCHSPEZIFISCHE GEOMETRIEN
„Wir bekommen immer mehr Kundenanfragen nach 3C-Werkzeugen mit hochspezifischen Geometrien, die etwa für die Bearbeitung von Glasgehäusen eingesetzt werden sollen“, erklärt Dold. „Für die individuellen Anforderungen an die einzelnen Werkzeuge der Kunden entwickeln wir dann die Bearbeitungs- und Programmierschritte unserer Lasermaschinen, um diese Werkzeuge herstellen zu können.“
„Kleinste Innenradien, Drehteile, Absätze und andere Geometrien lassen sich mit diesen Werkzeugen fertigen“, erklärt Dr. Gregory Eberle, Prozessspezialist Lasertechnik bei EWAG. In konventioneller Bearbeitung müssten Werkzeuge dieser Geometrien aus mehreren Teilen zusammengesetzt werden. Mit einer EWAG LASER LINE ULTRA etwa ließen sie sich vollautomatisiert und in einem Arbeitsschritt produzieren.
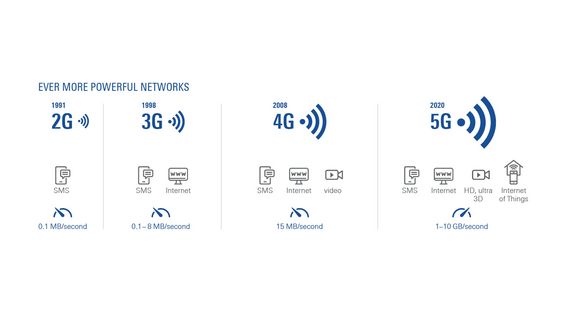
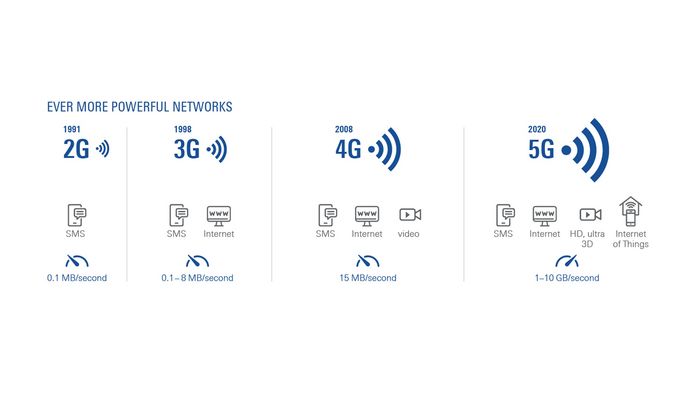
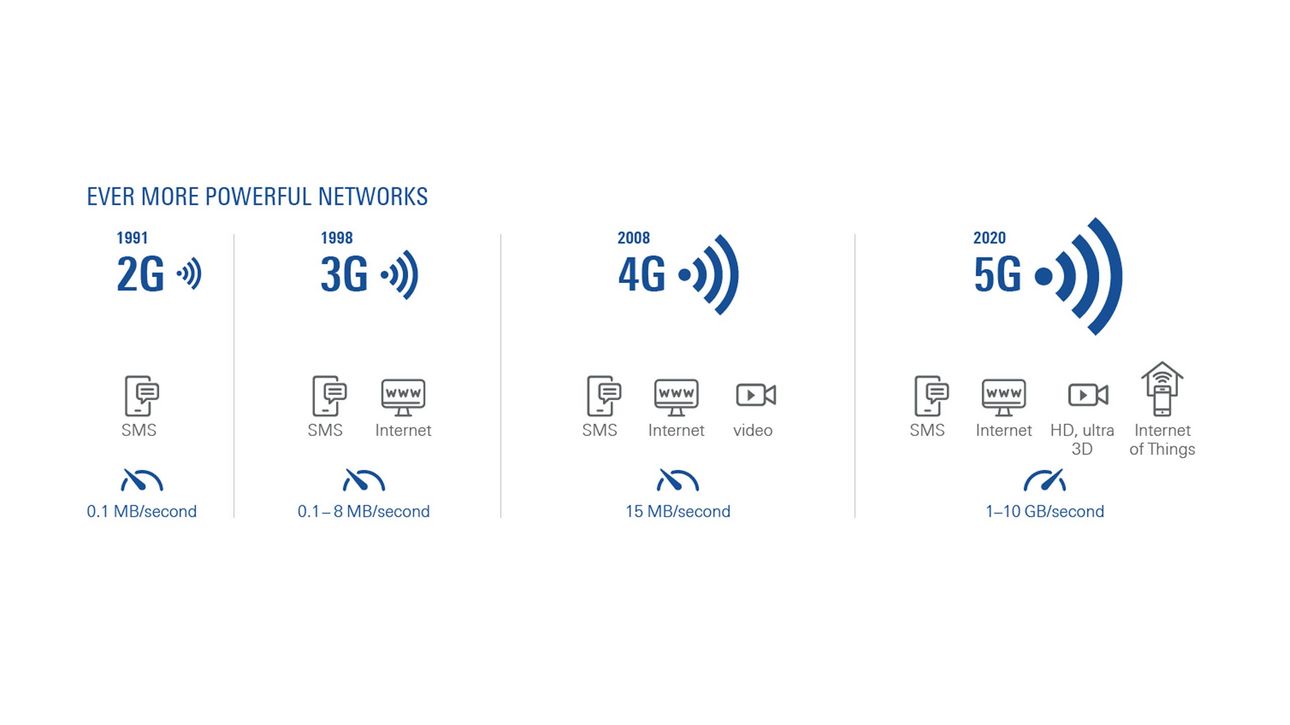