Wir haben uns auf den Weg gemacht
Mit der IMPACT 4530 hat die UNITED GRINDING Group die weltweit erste Additive Werkzeugmaschine „Made in Switzerland“ im Industrieformat entwickelt. CEO Stephan Nell erläutert im Gespräch mit Professor Markus Bambach von der ETH Zürich, welches Potenzial die neue Technologie hat.
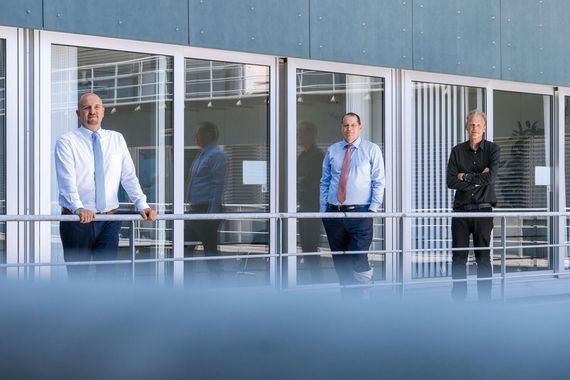
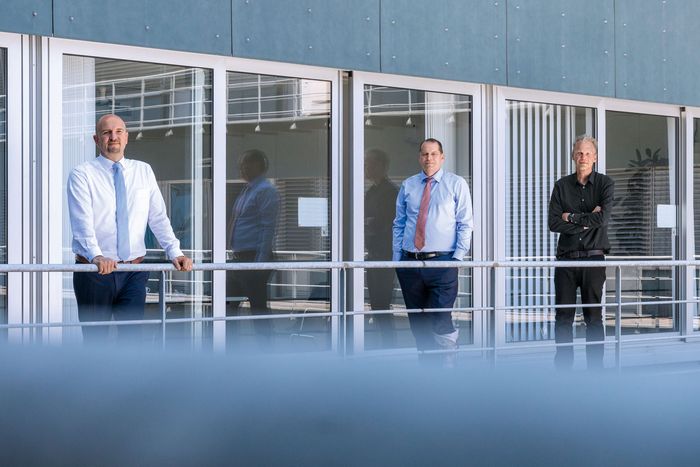
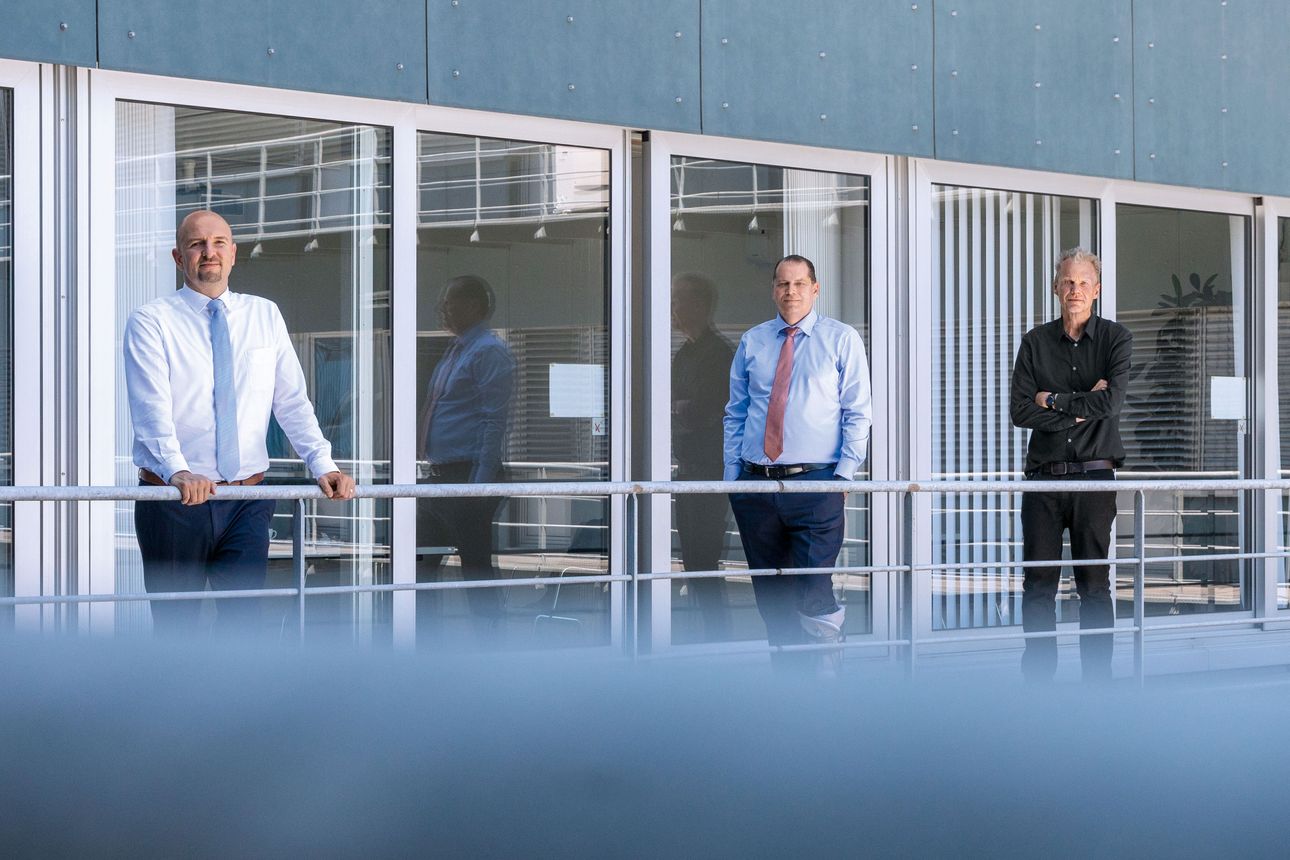
Herr Nell, strebt die UNITED GRINDING Group mit der IMPACT 4530 eine Technologieführerschaft in der Additiven Fertigung bei Werkzeugmaschinen an?
Stephan Nell: Wir wollen sicher vorne mitmachen. Es gibt viele etablierte Hersteller, die mit der Additiven Fertigung eine lange Erfahrung haben und damit gut unterwegs sind. Wir möchten aber unsere eigene DNA in das Thema einbringen, und dazu gehören eine hohe Zuverlässigkeit und Verfügbarkeit. Es geht weiterhin darum, die Kunden erfolgreich zu machen. Und das mit der besten verfügbaren Technologie.
Welches strategische Motiv verfolgen Sie damit?
Stephan Nell: Das additive Herstellen kann eine Fertigungsstufe vor dem Schleifen sein, und das geht in Abnehmerbranchen, die potenzielle Kunden für den 3D-Druck sein können. Und es ist natürlich ein neues Fertigungsfeld, das viel Innovation braucht. Denn Schleifen ist ja schon, das kann man ruhig sagen, ewig alt. Da geht es nur noch evolutionär vorwärts. Klar, es kommen immer neue Innovationen dazu, und die Maschinen werden immer besser. Aber es gibt keine neuen Riesenschritte mehr. Der 3D-Druck hingegen ist eine fundamental neue Technologie. Das hat uns interessiert.
Herr Bambach, ist denn heute schon absehbar, dass es sich bei der Additiven Fertigung um einen echten Technologiesprung handelt?
Markus Bambach: Ich denke schon, dass wir es hier mit einem Technologiesprung zu tun haben. Wenn man sich in die erste industrielle Revolution zurückversetzt, als die Webmaschine erfunden und später mit einer Lochkarte programmierbar gemacht wurde, so findet man über die Zeit viele Beispiele, wo Hardware- und Softwareinnovation Hand in Hand gehen, um dann einen Technologiesprung zu erzeugen. Das muss in der Additiven Fertigung genauso erfolgen – dass wir auf der Hardwareseite eine gute Maschine haben, aber auch die gesamte Kette auf der Softwareseite beherrschen.
Herr Nell, wie hat sich denn der Einstieg in das neue Technologiefeld konkret voll zogen, so etwas geht ja nicht per Beschluss von heute auf morgen.
Stephan Nell: Ja, das war ein Weg. Zunächst einmal sind wir in die Rolle des Kunden eines solchen Maschinenherstellers geschlüpft. Das haben wir mit Inspire gemacht – hier gab es schon seit 1996 Erfahrung mit 3D-Druck, und in dieses Netzwerk sind wir später mit dem Kauf von IRPD direkt eingestiegen. Und dann haben wir das Entwicklungsteam und die Inspire-Leute mit der 3D-Vorerfahrung auf den Weg geschickt und gesagt: Jetzt macht mal. Herausgekommen ist die IMPACT 4530 – 9,2 Tonnen Schweizer Maschinenbau.
Herr Bambach, ist die UNITED GRINDING Group hier nach Lehrbuch vorgegangen?
Markus Bambach: Ohne Zweifel, es gibt einige Unique Selling Points der Additiven Fertigung. Etwa dass die Kosten pro Bauteil unabhängiger von der Komplexität der Bauteile und von der Stückzahl sind. Das gibt es bei anderen Verfahren nicht. Zudem kann lokaler produziert und die Produktion dezentralisiert werden. Trotzdem müssen wir die Kostenstruktur immer in Fertigungsketten denken. Und wenn die Kostenfrage dominiert, dann hat man keinen Business Case mit der Additiven Fertigung, wie wir sie heute kennen. Denn häufig dauert es relativ lange oder benötigt sehr viel Erfahrung, bis überhaupt ein Bauteil gedruckt werden kann. Bei komplexeren Bauteilen und schwierigeren Anwendungen müssen Sie schon ein Ingenieurteam beschäftigen, bis Sie dann nach ein paar Wochen vielleicht tatsächlich ein Bauteil haben, das den Anforderungen genügt. Aber UNITED GRINDING hat jetzt eine sehr solide Maschine auf den Markt gebracht – auf einen Markt, in dem Sie ohnehin etabliert sind. Das sind sehr gute Voraussetzungen.
Herr Nell, Herr Bambach scheint der Technologie als solches noch etwas abwartend gegenüberzustehen.
Stephan Nell: Wir haben nie daran geglaubt, dass die Additive Fertigung das Schleifen ersetzen soll. Denn zum einem bietet das Verfahren nicht dieselbe Oberflächenqualität. Und auch die Präzision kann nicht mithalten. Aber wir haben damit einen neuen generativen Prozess, in dem das, was heute den Schleifmaschinen vorgelagert ist, ergänzt werden kann. Es ist eine von vielen Technologien, die unser bestehendes Portfolio gut ergänzen. Wenn Sie sich heute eine MÄGERLE-Werkzeugmaschine ansehen, die kann nicht nur schleifen, sondern auch fräsen und bohren. Sie ist ein Bearbeitungszentrum. Bei WALTER EWAG haben wir die Lasertechnologie aufgebaut. Viele wissen gar nicht, dass wir mehr Messmaschinen herstellen als allein darauf spezialisierte führende Unternehmen. In dieses Konzept passt auch eine Additive Werkzeugmaschine hinein.
Im Gespräch mit den jungen Ingenieuren bei IRPD in Sankt Gallen stand die Utopie im Raum, dass wir durch die Additive Fertigung insgesamt bessere Produkte bekommen. Wie weit träumen Sie diese Utopie mit?
Stephan Nell: Wo die Ingenieure recht haben: Die 3D-Fertigung gibt Konstrukteuren ganz neue Möglichkeiten. Die müssen zuerst einmal lernen, ein Teil so zu konstruieren, dass man die Vorteile des 3D-Drucks überhaupt mitnehmen kann. Es ergibt keinen Sinn, ein bestehendes Teil, das heute auf einer Fräsmaschine oder einer Drehbank gemacht wird, eins zu eins auf einen 3D-Drucker zu verlagern.
Markus Bambach: Wenn Sie einem Dienstleister, der sein Geld im Bereich Zerspanung verdient, eine 3D-Maschine hinstellen und da ist kein Konstrukteur – dann fällt es sehr schwer, zu besseren Teilen zu kommen. Denn er denkt eben noch in Konstruktionen, die er spanend fertigt. Erfolgreiche Beispiele, die ich aus der Industrie kenne, stammen hauptsächlich aus dem Bereich Hydraulik. Oder der Kühlung, wo statt vieler Einzelteile ein Integralteil gedruckt wurde. An solchen Beispielen kann man schön einen Technologiesprung sehen, bei dem das Potenzial systematisch gehoben wird. Zum Beispiel auch in der Luft- und Raumfahrt, wo extremer Leichtbau möglich ist. Dann können wir zur Medizintechnik schauen, wo individualisierte Komponenten wichtig sind. Aber wenn jetzt gesagt wird, wir bekämen als Gesellschaft bessere Produkte, da habe ich meine Zweifel. Die größte 3D-Serienproduktion, die ich kenne, sind ein paar Zehntausend Designerbrillen pro Jahr. Aber es können nicht einfach mal so zwei Millionen Teile gefertigt werden – da hat die Technologie ihre Grenzen.
Stephan Nell: Es gibt Grenzen, klar. Aber gleichzeitig ist auch ein Wandel im Gang. Bisher standen die meisten 3D-Drucker im Metallbereich in Universitäten und in Versuchsabteilungen von Unternehmen. Aber jetzt wollen die Kunden industriell produzieren mit den Maschinen und sind nicht am Optimieren von Prozessen interessiert. Die ass es funktioniert. Und den Anspruch erfüllen wir mit der IMPACT 4530.
Was sind denn genau die Ansprüche von Kundinnen und Kunden an eine industrietaugliche 3D-Druck-Werkzeugmaschine?
Stephan Nell: Sie muss stabil laufen, schnell arbeiten und darf keine Fehler machen. Deshalb verfügt die IMPACT über bis zu vier Laser mit je 1000 Watt. Die hinterlassen aber natürlich Schmauchspuren, damit muss umgegangen werden. Dann gibt es scheinbar simple Dinge: Die Lippe, die das Material verstreicht, wird bei uns überwacht und bei einem Defekt autonom getauscht, um zu vermeiden, dass es einfach weitergeht. Und dann ist es für einen Industrieprozess auch wichtig, dass der Kunde die Maschine nicht ständig mit Personal überwachen muss, das kostet Geld. Sie muss also eine hohe Autonomie aufweisen und sich weitgehend selbst überwachen. In der Regel wechseln Teile und Material, dem muss die Maschine gewachsen sein. Ich darf nicht ein oder zwei Schichten verlieren, nur um einen Materialwechsel zu machen. Bei uns dauert ein Materialwechsel nur 120 Minuten, und von Job to Job geht es in 15 Minuten. Zudem haben wir viele Kunden, die fräsen, die drehen, die schleifen, die haben viele Fertigungstechnologien im Haus und entsprechend viele Mitarbeitende. Die müssen den 3D-Druck entsprechend integrieren. Also muss ich die Maschine so konstruieren, dass keine Kontamination der Umwelt stattfindet. Denn Menschen dürfen nicht in direkte Berührung mit dem Metallpulver kommen.
Das klingt doch nach dem richtigen Weg. Vielleicht könnten die Utopien doch wahr werden, was meinen Sie, Herr Bambach?
Markus Bambach: Vielleicht, wenn sich die Additive Fertigung als Technologie noch weiterentwickelt. Aber dass sie sozusagen eine Ersatztechnologie für etablierte massenproduktionstaugliche Technologien wird, das sehe ich erst mal nicht. Wichtig ist auch die Weiterentwicklung der Softwarelösungen.
Stephan Nell: Ich finde es schön, wenn man sich an Utopien orientiert, und die Softwarelösungen optimiert das IRPD-Team in Sankt Gallen übrigens ständig weiter. Am Ende ist es für die meisten Kunden eine Effizienzfrage. Hier spielen inzwischen auch ökologische Gesichtspunkte eine große Rolle. Da hat die Additive Fertigung sehr viel Potenzial. Man muss weniger transportieren, und die Lieferketten werden kürzer. Ich bin überzeugt, dass die Additive Fertigung ihren Weg in die Werkzeugmaschinenindustrie finden wird. Aber sie wird dabei nicht alles andere verdrängen oder ablösen.
Im Gespräch
Text: Michael Hopp, Fotografie: Thomas Eugster