Completely new possibilities in grinding with metal bonded CBN and Diamond wheels
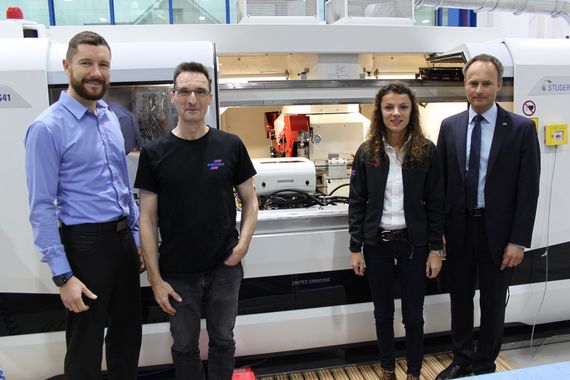
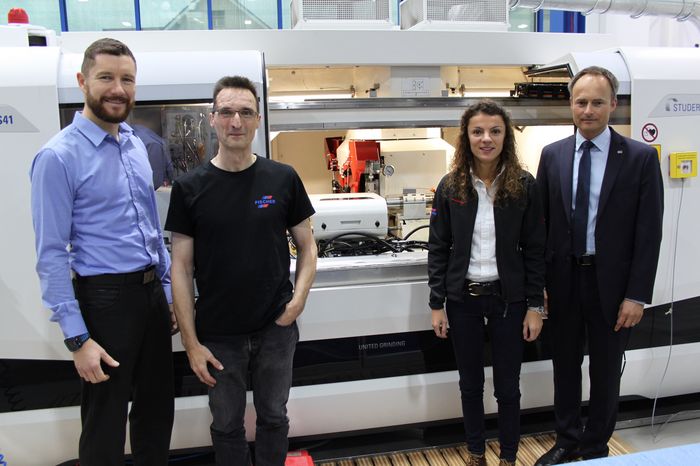
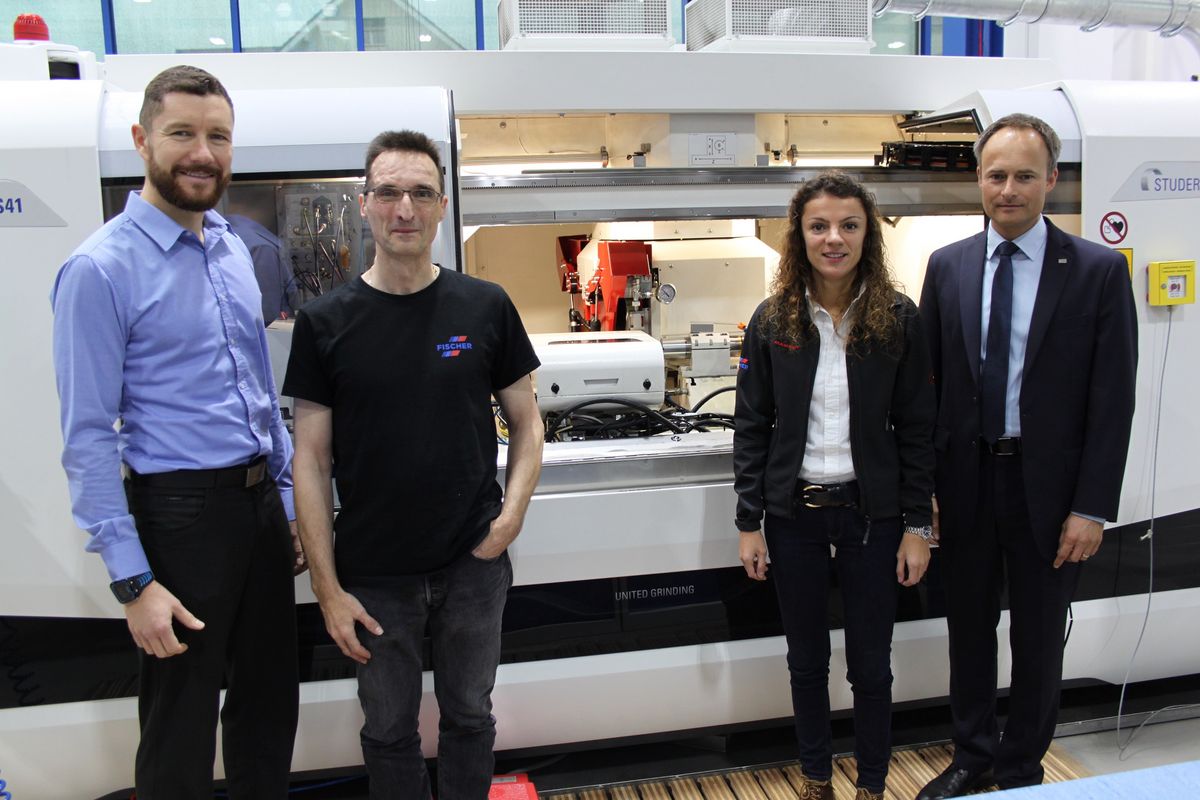
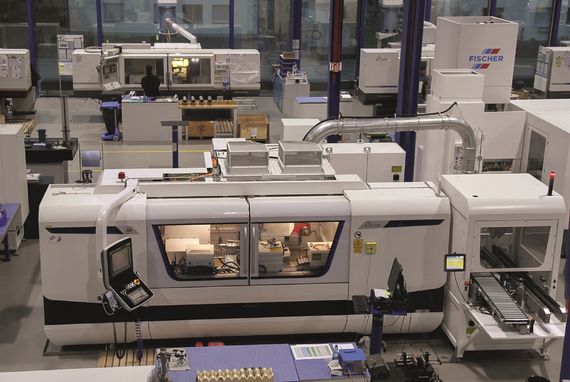
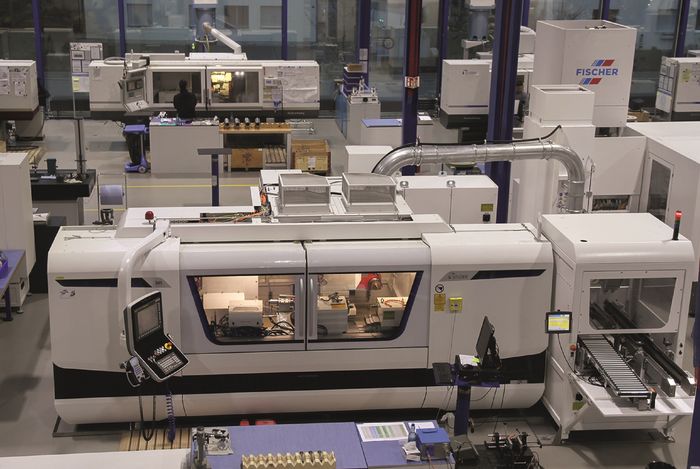
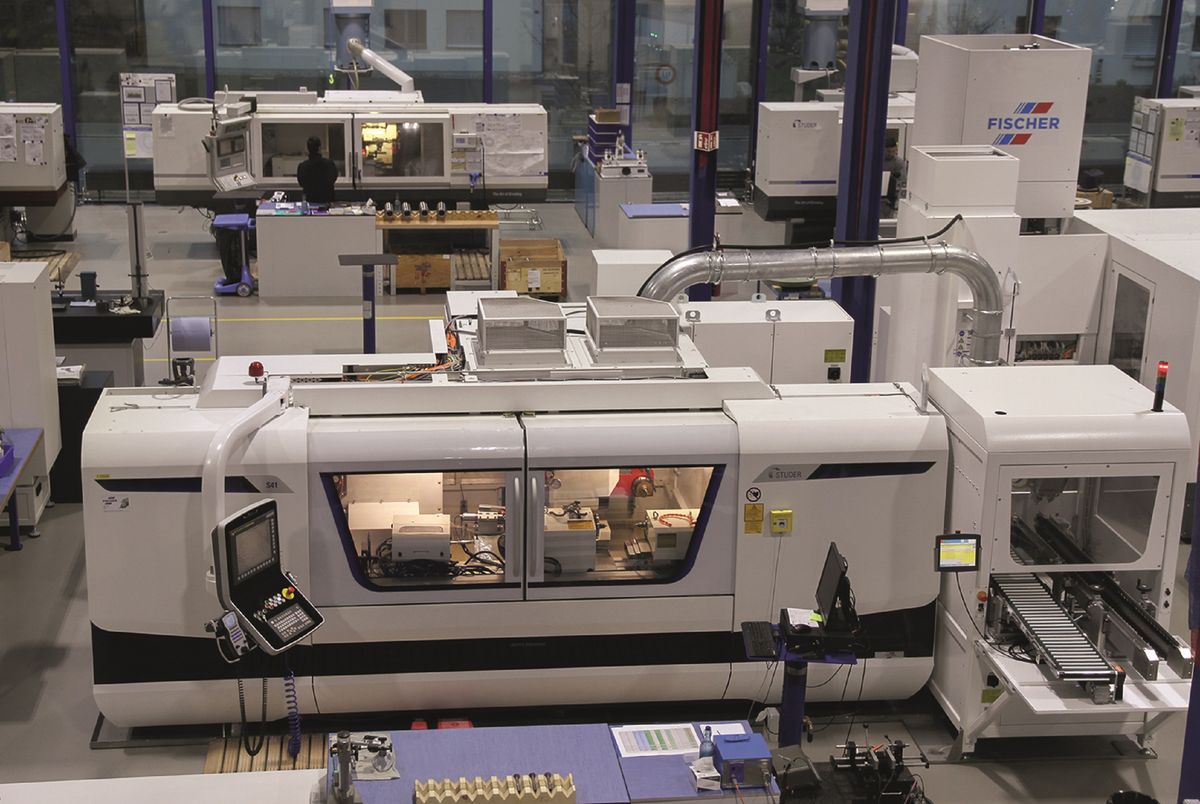

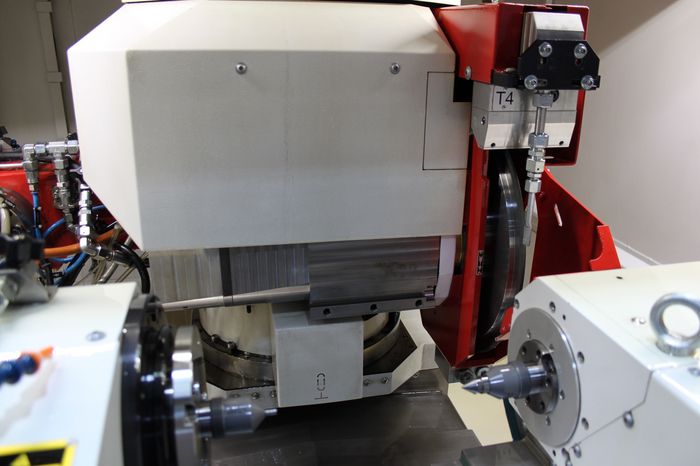
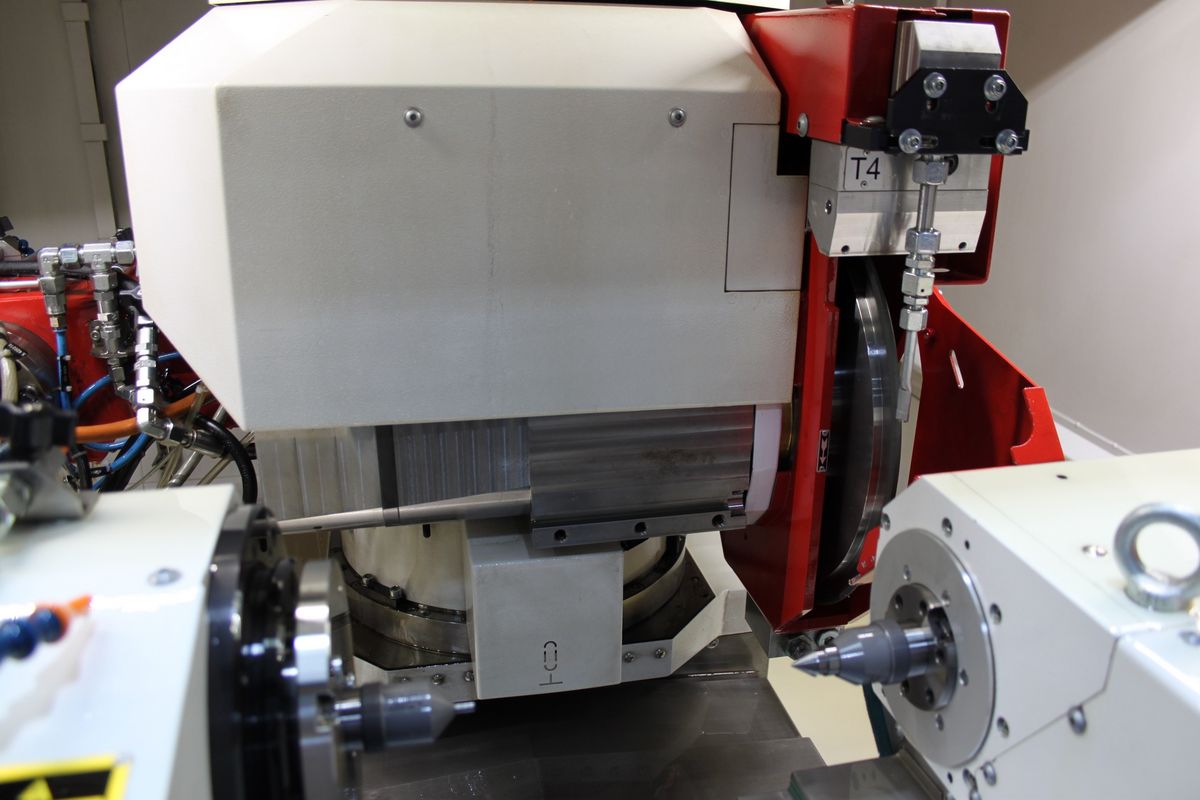
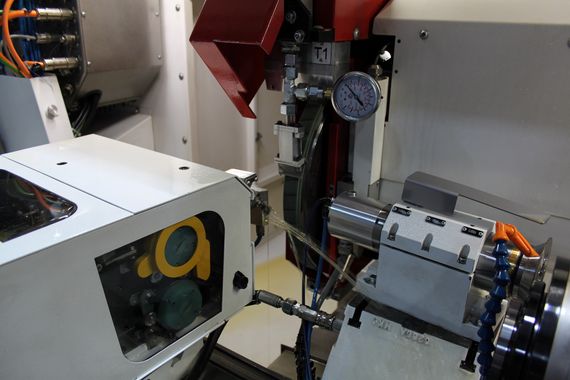
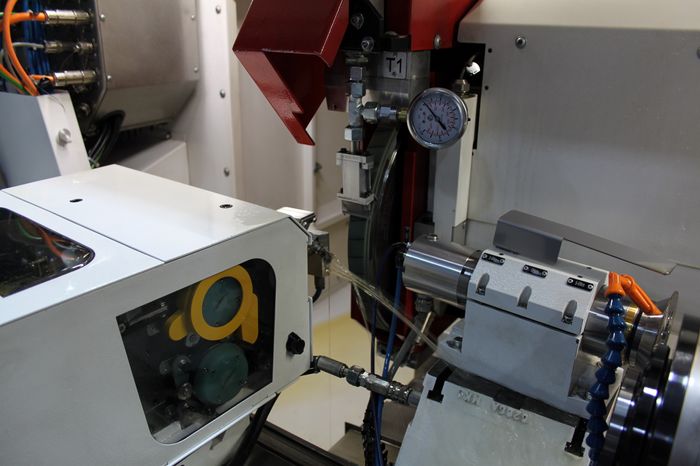
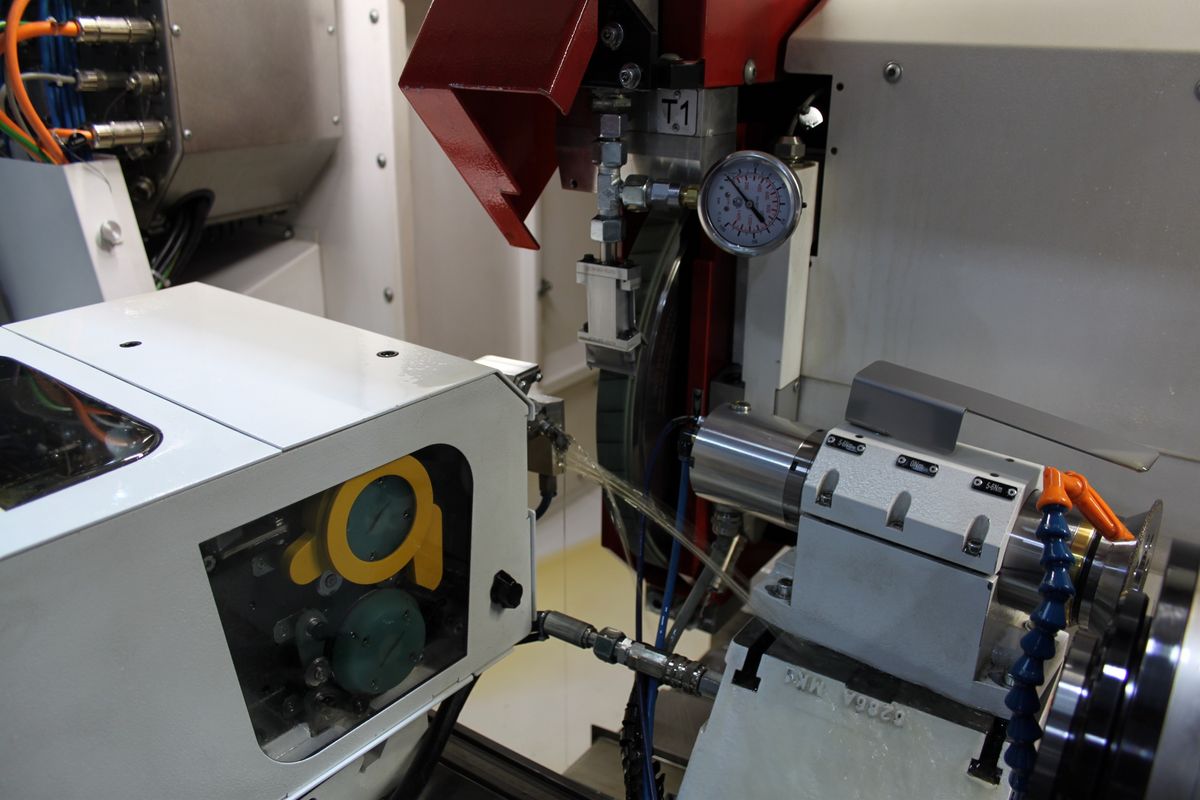
This is made possible by WireDress® from STUDER. Not only does this innovative, electro erosive integrated dressing technology save massive downtime, it also enables sintered metal bonds to be dressed with the highest precision in the grinding machine at full wheel speed. Fischer AG in Herzogenbuchsee, manufacturer of high-precision spindles, has been using this technology for several months and cannot hide their enthusiasm.
Alfred Mair, Head of Grinding Technology at Fischer in Herzogenbuchsee, faced a challenge. The aim of Fischer AG was not only to increase productivity, but they also reached their limits in the grinding of exotic materials such as titanium and hard-to-machine hard materials under the increasing quality demands from the customers. He could not solve the problem with a conventional grinding machine. What next? The solution was found by Mair at STUDER. Here the CNC universal cylindrical grinding machine S41 is manufactured. Specifically designed for large workpieces, it has a length between centres of 1000/1600 mm and a centre height of 225/275 mm. It processes workpieces with high precision up to a maximum weight of 250 kg, just as effectively as small and medium-sized workpieces. But the key for Fischer is the fully integrated WireDress® dressing system. "We had high hopes that we could use metal-bonded grinding wheels for a measurable and reproducible highest quality, have a higher productivity, more universal machining options as well as reduced tool costs," Mair explains his expectations.
Expectations exceeded
STUDER configured the S41 with WireDress® based on additional wishes of Fischer AG. Thus, the machine received a special high-speed external grinding motor spindle, an innovative proprietary product of Fischer AG, in which the axial growth is particularly small. In addition, the spindle is tapered at the rear end, avoiding possible collision situations. This is a specific benefit for face/shoulder grinding with the spindle at an angle. The S41 is supplemented with a fully automatic workpiece magazine and handling system, which ensures fully automatic series production of the high-quality precision components in a stand-alone operation. The conclusion of Mr. Mair after a solid introduction time of the machine: "I am blown away”. Three to five times faster than with conventional technology, with absolute reproducibility, ground in a tolerance range of less than 1μm! I have never seen anything like that! I am extremely impressed. "
The secret behind it
But how does this dressing technology work? Michael Klotz, project manager for development at Fritz Studer AG, explains it this way: "It is a well-known fact that metal-bonded grinding wheels are much more durable and dimensionally stable when machining difficult-to-machine materials and ultimately enable higher productivity. The problem with this is that metal bonds can only be dressed to a very limited extent using conventional methods in the grinding machine. In addition to this there is a high dressing tool wear associated with a low cutting ability. This is neither an operator-friendly, nor a high quality and process consistent dressing method”. That's why the "best" bond – the metal bond - is rarely used. "STUDER has developed, along with technology partners, the machine-integrated WireDress® dressing technology. Here, the dressing is done at full wheel speed. In contrast to conventional mechanical or external EDM dressing, WireDress® dressing occurs by a modified wire erosion in the grinding machine, where the grinding oil serves as a dielectric.
The dressing process is contactless and wear-free. The grit itself is not dressed, the metallic bond around the grit is removed. Depending on how deep the grit is embedded in the bond, it either falls out or remains with original sharpness in the bond. The grinding wheel receives a high grain clearance for maximum cutting capability, lower grinding forces and low burning risk. You can now harness the capabilities of metal bond with WireDress®. Using a bond with a high dimensional stability, almost any profile can be precision-contoured in the μm range. Long dressing intervals can be achieved. Yet another plus: the accurate processing of sophisticated or smallest geometries that was neither economical nor possible before, now becomes feasible. Compared to grinding with ceramic-bonded grinding tools, significant increases in productivity in the range of at least 30 percent is realistic, with resin bonds, even more is possible. With a sintered metal bonded grinding wheel, you can even go beyond the limit - you can just re-dress it in the machine again. With a conventional grinding wheel you can only go over the limit once. "Maximize these limits without fear - that also makes greater profitability possible," adds Michael Klotz.
Several factors for success
"If you have the right technology, the process is peanuts. In the past, you had to feel your way, today everything is process-stable. This also has the advantage that you can calculate the costs more clearly, "explains Mair. He also knows that the right technology is not just about the machine. What other factors also contribute to reproducible manufacturing in the absolute range of less than 1 mu? "A fully air-conditioned hall, which among other things also ensures the thermal stability of our spindle, the right tooling, state-of-the-art measuring technology, optimized cooling and, of course, highly trained and motivated staff," says Mair.
Conclusion
For Fischer AG, the investment in the S41 has paid off with WireDress® technology. The productivity could even be increased by 70% for certain materials. Mair states further: "I am convinced that if this technology gets around in the professional circles, STUDER will be flooded with orders."
Another advantage that should be of interest to engineers and design engineers in particular: not only can straight forms be dressed, but also very fine profiles, which was previously not possible with metal-bonded grinding wheels. This opens completely new design possibilities for engineers, and even unimaginable horizons.