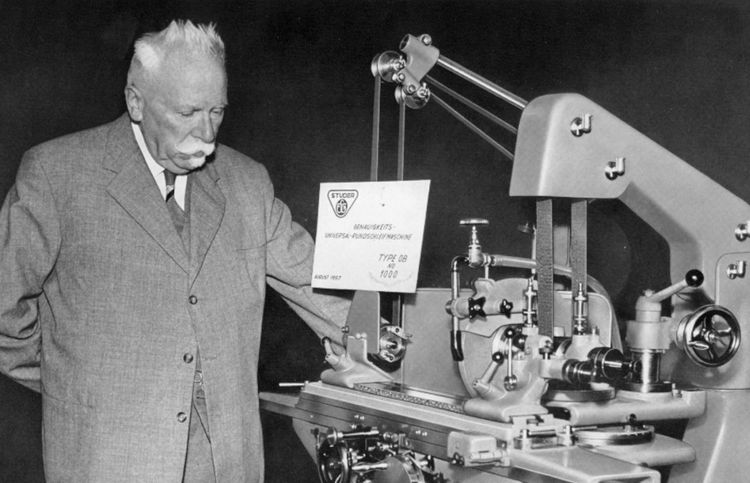
Did you know that grinders were first used as far back as 4,000 years ago? Our ancestors ground holes in stone axes and hammers. In ancient Greece, techniques for cooling grinding stones with oil or water were used.
One major leap in grinding technology came in the 15th century with courtesy of Leonardo da Vinci. He invented a needle grinder with automatic loading and unloading of the needles. It took until 1874: in that year Brown & Sharpe marketed the world's first cylindrical grinding machine. Workpieces could then be manufactured with a precision of up to 0.01mm (0.0004").
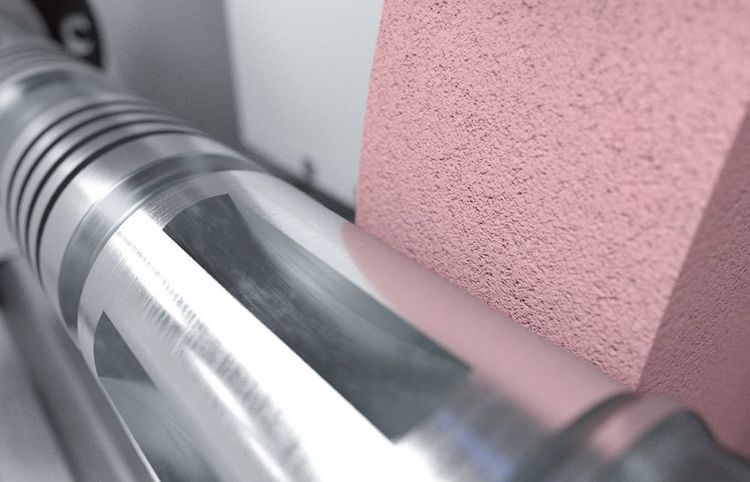
Grinding is an abrasive machining process used for fine machining and finishing of workpieces. It can be performed manually or using grinding machines. As with all abrasive procedures, excess material is removed from the workpiece in the form of chips. The cutting is actually performed by the edges of microscopically small hard mineral crystals in the grinding tool.
Grinding meets today's production needs as it guarantees high quality and output at reduced cost per workpiece. Grinding is available for:
- High dimensional and form accuracy
- A defined surface quality
- Machining of difficult-to-cut materials
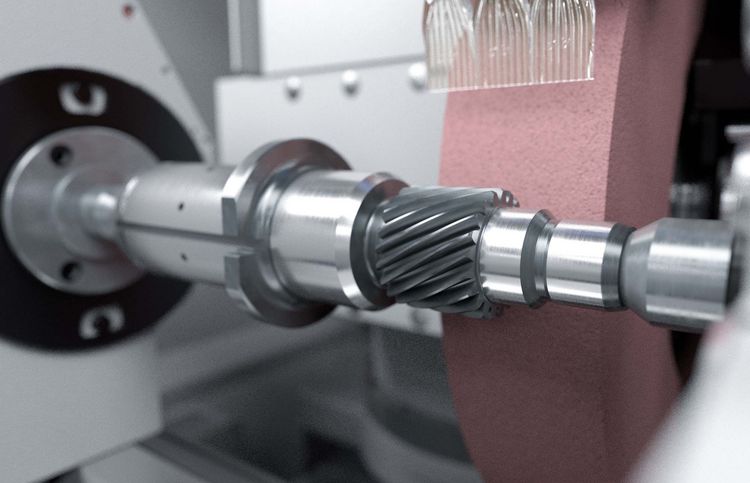
External cylindrical grinding is used for the production of cylindrical or tapered workpieces, such as the grinding of shafts, axles and spindles as used in the general machine tool, automotive and aerospace industries. The circumference of the grinding wheel is used to remove material from the circumference of the workpiece. This can be done in the radial (plunge grinding) or axial (traverse gringing) modes. To allow for greater accuracy in clamping, workpieces are usually mounted between centres. Multiple idle strokes (spark-outs) are used to improve the form accuracy and surface quality.
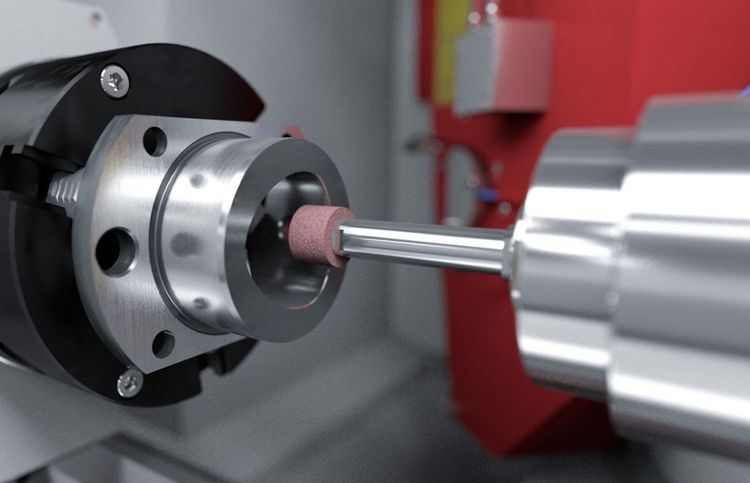
Internal cylindrical grinding is primarily used for machining cylindrical or tapered bores. During internal cylindrical grinding, the longitudinal feed movement is typically carried out by the grinding wheel, with the radial infeed movement during internal cylindrical grinding handled by the wheelhead or the workhead, depending on the design of the machine. Basically, the same kinematic relationships apply as with external cylindrical grinding. The contact area between grinding wheel and workpiece is however considerably larger, which makes the removal of chips and the cooling of the process more difficult.